Knowledge
What is Adhesion?
Contents
The Fundamentals of Adhesion
Materials, substances, and the objects they make up stay together and stick to each other for a simple reason: the molecules they are made of attract each other. The attraction between molecules is ultimately based on the attraction between the negative charges and positive charges of the electrons and protons that make up the atoms and molecules: at the atomic level, these are electrostatic forces.
Cohesion is the tendency of substances to stay together due to these cohesive forces.
Adhesion is the action of these same attractive forces between dissimilar materials that hold a bonded joint together.
In manufacturing, adhesive bonding takes many forms, but the principles of adhesion are the same. Even if the application is metal joint welding, gasket sealing with glue, implantable medical device coating, inkjet printing on plastic film, or automotive painting, successful adhesion relies on the understanding and control of three distinct yet interrelated elements.
The 3 properties that must be controlled for successful adhesion include:
- The composition of the adhesive, coating, ink, or paint
- The application of the adhesive, coating, ink, or paint
- The quality of the bond surface
Each of these presents its own challenges to control, but the first two have been well understood and defined by the suppliers of the adhesives and dispensing equipment. The third element is influenced by the widest array of variables and goes through the most changes without detection.
How Can Surface Intelligence Assist Your Manufacturing Process?
Contact a Surface Analyst Expert today to learn more about our expertise, technology, and other services:
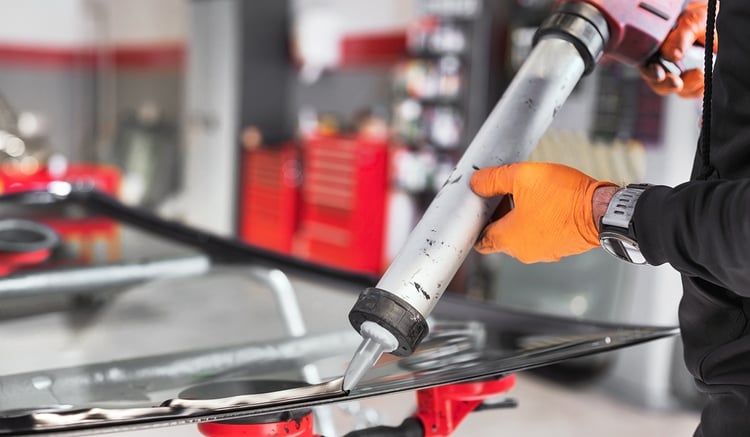
Important Definitions Related to Adhesion
What is a Surface?
A surface (as it relates to adhesion) is the uppermost few layers of molecules comprising the free surface of a substance. It’s the properties of these few molecular layers that determine if an adhesive or paint will stick or release (fail).
The properties of the molecules that make up a surface are generally very different from those that make up the bulk of a material. The surface is always more reactive than the bulk for the reasons discussed below. Because of this, the composition and properties of a surface are very sensitive to its history and its environment.
Every operation, equipment, the people who handle the material, and even the air in a production facility can dramatically affect the composition and properties of a surface and determine whether or not a particular bonding or coating operation will succeed.
What is Surface Energy?
Every atom and molecule attracts another atom or molecule to one degree. The substance will aggregate and form a liquid or a solid if the attraction is strong enough. If the attractions are weak, these attractions may only become evident when the substance is cooled enough for the atoms or molecules to aggregate (think of liquid nitrogen or liquid helium). These attractions include the electrostatic forces like weak van der Waals forces or strong ionic bonds, along with the covalent forces that come from atoms sharing electrons to form molecules. These are the cohesive forces responsible for the cohesive properties of a liquid or a solid, including stiffness, strength, and viscosity.
Below the surface of a substance, say more than about three or more molecular layers away, atoms and molecules are completely surrounded by neighboring atoms and molecules, and the attractions that they feel due to van der Waals, covalent, and ionic bonds are balanced in all directions.
Atoms and molecules in a surface are in a very different situation. They don’t have any nearest neighbors towards the surface, and so the forces are unbalanced. This gives rise to the property called Surface energy, which is an expression of the tendency of a surface to have higher reactivity than the bulk. Because of surface energy, surfaces adsorb oxygen and water vapor from the air; they also adsorb any other airborne molecules in the environment, like oil vapors. This adsorption is because the molecules in the surface attract the molecules in the environment by the same cohesive forces that attract them to their nearest neighbors: van der Waals, covalent, and electrostatic (ionic) attractions.
Hard materials like metal, ceramic, and glass tend to have high surface energies. The surfaces are chemically reactive, so they quickly oxidize when exposed to air. They also tend to adsorb contaminants very strongly. When clean, they adsorb paints and adhesives very strongly and therefore form strong bonds. Soft materials like polymers tend to have relatively low surface energies: the surfaces are not very reactive and don’t tend to adsorb other molecules very strongly. They tend to be more difficult to bond with adhesives unless given a surface treatment like a corona, flame, or plasma treatment to increase the surface energy.
What is Surface Tension?
All liquids and solids have the property of surface energy. The surface energy of a liquid is usually referred to as its surface tension. Scientists usually speak of surface energy as energy per unit area (millijoules per m2); manufacturing engineers frequently use units of surface tension (force per unit length, or dyne/cm). Both units are dimensionally equivalent.
Further Reading:
Discover the differences between surface tension and surface energy here. Or learn how surface tension is measured.
Adhesion and Cohesion
A bonded joint is a structure designed to transfer stress from one substrate to the other. The load path is from substrate → interface → adhesive → interface → substrate (See Figure 1).
Figure 1: Referenced in the article, "The Benefits of Benchmarking Surface Quality in Manufacturing."
If the joint is loaded to failure, these are the 5 places where failure can occur. If the failure occurs in either substrate or in the adhesive, it’s termed a cohesive failure. This sort of failure is predictable based on the materials' cohesive properties (strength and toughness). A well-constructed joint will always fail cohesively in either the adhesive or the substrates. Confidence in a cohesive failure mode allows engineers to confidently specify the joint design based on the material properties.
If a bonded joint fails at the interface, it’s termed an adhesive (or interfacial) failure. Adhesive failure is a sign of poor surface preparation. Because a joint constructed from poorly prepared substrates doesn’t have a predictable strength or toughness, engineers can’t design a reliable structure unless they can be confident that the bonded joints will always fail cohesively. A bonding process must be designed and executed to guarantee that interfacial failure will never occur.
Joints between similar materials that are formed by solvent welding or melt bonding don’t have well-defined interfaces. These structures depend on the diffusion of one material into the other, and the joint properties are determined by the cohesive properties of the zone of interdiffused substances.
It is the chemical interactions at the interface of the adhesive and substrate that we call adhesion. If we look around us with an eye for all the places where one material is sticking to another, whether it’s the protective seal on a medicine bottle (See Figure 2), the padded dash in your car, or the display on your laptop computer, we quickly come to understand that adhesion science is critical for all industries and can teach us valuable lessons to enable better product development.
To further enhance your product development teams and strategies, apply a top-down method, further explain in our eBook: "The Advanced Guide to Transforming Product Development Through Surface Intelligence Data & Technology."
Figure 2: Protective seal located on a medicine bottle, confirming the contents inside have not been tampered with.
What is Materials Science?
Adhesion science can be considered a branch of the broader field of materials science. It deals with understanding and controlling the properties of things whose performance depends on the interface between two materials. An appreciation of adhesion science leads to the design and manufacture of longer-lived products with improved performance.
The Materials Science of Adhesion Includes:
- Developing an understanding of the chemical interactions that make two things adhere to one another
- Using this understanding, along with a knowledge of materials chemistry, to design and synthesize adhesives, paints, coatings, and ink
- Sometimes, using this understanding to develop things that don’t stick: release coatings, non-stick cookware, mold releases
- Using this understanding, along with a knowledge of materials chemistry, to design and synthesize adhesives, paints, coatings, and ink
- Furthering the physical design of adhesive bonds to create the most efficient (i.e., lightweight, high-performance) structures while avoiding failures due to stress concentrations, etc.
Does Surface Roughness Impact Adhesive Properties?
Many people believe that the ‘mechanical interlocking’ of an adhesive or coating with the nooks and crannies of a rough surface is necessary for a strong adhesive joint. However, adhesion relies on atomic forces, specifically intermolecular attraction, which are not affected by surface roughness. Roughness can enhance a bond that is already strong by providing a tortuous path that interferes with the ability of a crack to propagate, but no amount of roughening will create a good bond without strong adhesion in the first place.
Does Roughness Increase Your Adhesive Bonds?
Watch how contact angles challenge the age-old myth:
To immediately see that roughness is not an important factor in adhesion, simply open up any electronic device and look at the structure of the microelectronics inside. These depend on establishing strong and durable adhesive bonds between the atomically smooth surfaces of the semiconductor devices and the circuit boards they reside on. If surface roughness were critical for adhesion, these devices would fall apart.
But why is the most common instruction that adhesive manufacturers put on their technical datasheets to roughen the surface prior to bonding? The act of roughening with an abrasive primarily removes gross levels of contaminants and loosely adhered oxides and dirt from the surface, thereby creating a clean, strong, chemically active surface: this is actually enhancing the adhesion.
If we take this nicely cleaned, roughened surface and simply apply a monomolecular layer of silicone to that surface, we have not changed the roughness a bit, yet we have created a surface that is impossible to bond to. The silicone interrupts the chemical interactions that we need between the adhesive and substrate in order to establish good adhesion. Roughness can enhance a bond that is already good—but roughness by itself cannot transform a bad bond into a good one. In order to create successful bonds/coatings, you need a clean, chemically active surface, not a rough one.
Further Reading:
Does Roughness Increase Your Adhesive Bonds?
Watch how contact angles challenge the age-old myth.
Knowledge of Adhesion Advances Innovation in Product Development
Adhesion science has taught us that the chemical interactions occurring within the interface's top 3-5 molecular layers are critical in establishing strong, durable, high-performance interfaces in bonded, coated, and printed structures.
Developing an appreciation for the advances in adhesion science helps product development teams leverage adhesive chemical bonding and advanced coatings to make efficiently manufacturable realities out of the most advanced and creative designs.
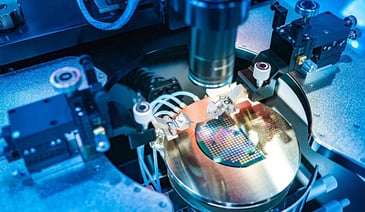
Further Reading:
Read this article to learn how you can boost product innovation using materials science & technology.
How to leverage adhesion science by changing from a mechanical mindset to a chemical mindset.
Contact Angle as a Quantitative Measure of Surface Energy
Contact angles formed by a liquid like water with a surface provide sensitive, quantitative data about the cleanliness and surface composition at a molecular level. A water contact angle is formed between the surface of a water droplet and the surface it is resting upon.
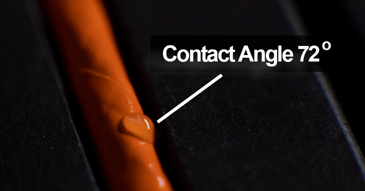
Measuring contact angle is a powerful surface characterization method for determining whether an adhesion process like coating, painting, printing, soldering, welding, and bonding will be successful. Contact angles are also used as surface cleanliness validation checks after cleaning processes to ensure these processes aren’t drifting out of spec and delivering consistently clean results.
Design Intelligent Surface Management
Throughout the Product Development Process
Brighton Science has deep expertise in adhesion, materials science, and manufacturing. Our goal is to help product development teams learn more about harnessing the power of adhesion in their new product development processes.
Discover how to leverage successful adhesion to develop superior products and gain a competitive edge by reading "The Brighton Science Advantage: Optimizing Manufacturing for a Competitive & Sustainable Future."