What is Dyne Testing?
Contents
Dyne testing is a method for measuring the wetting tension of a solid by determining the minimum surface tension of a specific liquid mixture that allows it to remain spread on the solid’s surface. This approximates the amount of energy required to spread other fluids across the surface and is expressed in units of surface tension (dynes per centimeter, or dynes/cm). This technique is outlined in ASTM D2578, "Standard Test Method for Wetting Tension of Polyethylene and Polypropylene Films."
The higher the dyne/cm value achieved, the higher the wetting tension of the solid surface. Higher wetting tensions, which approximate surface energies, are generally associated with higher rates of successful adhesion.
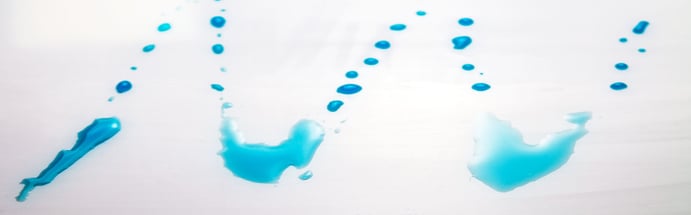
Although the technique is only considered appropriate for polyethylene and polypropylene films, for years, dyne testing has been the prevalent approach to assessing the cleanliness and surface energy of a wide range of material surfaces in terms of quality. Their widespread use and affordability have made them a popular choice among manufacturers despite their lack of precision, potential damage to material surfaces, and risk to users. While the science supporting dyne measurements as outlined in the ASTM standard is reliable, their application in a manufacturing setting and on other materials does little to avert or mitigate adhesion failure.
Dyne testing is based on the concept of surface energy or wettability, a process directly related to a surface’s adhesive potential. When a substance interacts with a substrate or material, it can reveal information about the material’s surface energy. The response of the dyne solution will vary depending on the surface energy.
When a dyne solution is applied to a surface, it can either form a continuous film or break up into droplets. The user makes this evaluation, and depending on the way the solution is applied, the condition of the applicator, the surface texture, lighting, and contrast, etc., it can be a rather subjective decision. If beading occurs, this signifies lower wetting tension in the material compared to the solution. Conversely, if the dyne solution remains a continuous film, the material possesses a higher wetting tension than the solution. This test, in theory, will tell the user the material’s dyne level.
Download Your Personal Copy of This eBook
Fill out the form to receive your personal copy of the eBook, "What is Dyne Testing?"
Download the eBook Here
How is a Dyne Test Conducted?
Dyne testing is typically used to gauge the wetting tension of non-absorbent, polymer-based materials. Dyne test solutions typically come in a set with a surface tension number associated with each dyne test pen or dyne test ink.
- The initial step involves selecting a dyne test pen filled with a test liquid assumed to have lower surface tension than the test sample. The pen is then used to gently spread a thin film of ink across approximately 1in2 (6.5 cm2) of the test sample’s surface. The user then notes the time required for the film to break up into droplets. If the time is more than two seconds, the test is repeated with a higher surface tension fluid.
The ‘precise’ wetting tension (referred to by some as 'dyne level') is considered to be equal to the highest surface tension dyne fluid that stays spread for at least 2 seconds before breaking up into droplets.
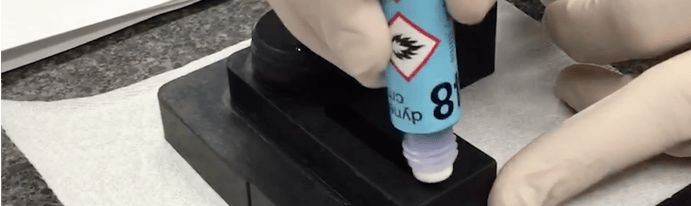
- Manufacturers utilizing dyne testing will often create a specification based on their adhesion goals and correlate it to a dyne level. Then, they will apply that dyne test pen number to a sample off the production line. A technician who applies the ink with the agreed-upon number does a visual check; if they think the ink appears to wet out enough, they will ‘pass’ the test and allow the part to move forward with the subsequent process step.
- To have validity, the test needs to be performed on a flat, clean (untouched) surface. It’s also recommended to perform the test on at least three distinct places on the sample.
- Safety measures should be followed to limit worker exposure to the hazardous chemicals found in dyne pens and solutions.
- Common dyne test solutions include dyne test pens and dyne test ink. Dyne test ink can be applied using clean cotton applicator swabs, brush applicators, and pens.
ASTM & ISO Standards for Dyne Testing
The primary benefits of this approach, grounded on the ASTM standard test method D2578-84 and ISO 8296, are the ability to conduct the test quickly and, in theory, easily, on the production floor.
These standards outline the procedure for determining the wetting tension of polypropylene and polyethylene film and sheeting only. These specific guidelines should be followed to achieve the most consistent and reliable results on material surfaces. It's well-known, however, that significant variation occurs between technicians even when evaluating the same materials [see, for example, R.J. Caimi, L.K. Derr, T.J. Dunn, Precision of the surface energy test, Converting Magazine, 10 (6) (1992) 62.].
This picture shows a series of dyne solutions applied to a uniform piece of material. Which would you consider to be the highest surface tension fluid that remained spread out? 40? 44? The behavior of 42 looks a lot like 48 or 50. It can be difficult to reach a confident conclusion.
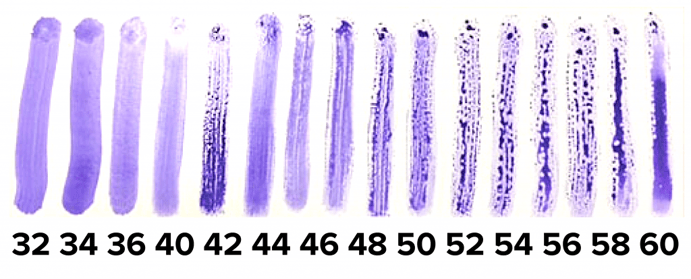
Common Uses of Dyne Testing
As mentioned, dyne testing was specifically designed for polyethylene and polypropylene films. While employing this procedure and the specified chemicals for films made from different polymers can be feasible, the user must determine the suitability and importance of using materials other than a polyolefin.
Dyne testing is commonly used in manufacturing environments where materials are tested before adhesion processes like bonding, sealing, coating, painting, and printing.
Another common use is validating material surfaces after surface treatment processes like corona treatment, flame treatment, and plasma treatment.
Limitations of Dyne Testing
Not all Dyne Tests Are Created Equal
Producers have observed discrepancies between the different brands of dyne pen manufacturers, making it impossible to equate one surface tension number across all brands. This inconsistency makes it challenging to understand precisely what the pens offer and whether they provide the necessary information. Additionally, some brands offer a broader range of numbers than others, implying that the required numbers for your surface might not even be accessible.
Human Error
As implied above, there is a significant human element involved in applying dyne solutions and in interpreting the results. One issue might be the inconsistency of application details when using cotton swabs. For example, the amount applied to the swab or to the surface of the swab can (and does) alter the test results. The application technique (pressure, velocity) when using a cotton tip varies from one individual to another and affects the response.
Any soluble contaminants on the surface impact the test results, as well. These contaminants could be impurities present on the material’s surface or, in the case of dyne pens, absorbed into the pen tip from a previous test. Polymer additives that bloom to the surface (antistats, slip agents, internal mold releases) are all soluble contaminants that alter the outcomes. Utilizing dyne pens, all impurities that are rolled over will be absorbed into the pen’s felt, thereby contaminating the tip and permanently altering the way the ink interacts with the surface, similar to dragging a yellow marker through blue or purple marker ink.
The ink determines a pass/fail level, and these results are based on the user’s interpretation of how the ink reacts to the surface, making the process very subjective. The nature of the test requires choosing only two outcomes for a given ink: either it beads up, or it wets out. If the users’ perspectives on what constitutes the thresholds for these properties differ, they might give a misleading positive or opt for a different pen when there’s no need. Interpretation can be made even more difficult depending on the color and texture of the material being tested.
Substantial training is crucial to accurately interpret the behavior of dyne ink on a surface and make a well-informed judgment on the next steps. However, even among trained operators, variability still exists [see above reference to round-robin study]. This training should also incorporate knowledge about the impact of the ink on the material’s surface.
These variabilities leave a lot up for human error.
Destructive to the Part & the User's Health
Dyne inks contain a blend of at least two solvents, which include VOCs, also known as “volatile organic compounds.” VOCs are recognized for their damaging effects to the environment and potential harm to those who handle them. Non-toxic dyne ink compositions based on water and alcohol are available, but because they rapidly change composition due to evaporation of the alcohol component, they are even less precise than the more common formulations based in part on formamide and 2-ethoxyethanol.
Not only is dyne ink potentially damaging to the user, but it is considered a destructive test. Once a dyne test has been conducted, the part is rendered contaminated and unsuitable for further production use. This increases the rate of product waste and does not permit 100% inspection.
Polymer Testing vs. Testing Other Materials
As mentioned, the ASTM standard for dyne testing is based on examining non-absorbent polyolefins: polyethylene and polypropylene films. The standard makes clear that using dyne tests on any other material should be studied comprehensively prior to use in order to ensure repeatability and reliability.
The Impact of Solvents
Many film manufacturers include slip agents in polymer formulations. These are lubricants that bloom to the surface and reduce friction as the film passes through processing equipment. If too much is present on the surface of the film, these compounds can interfere with the surface treatment and adhesion of printing inks and adhesives. Slip agents are readily soluble in many solvents, including those found in dyne solutions. As a result, dyne pen inks simply dissolve slip agents without detecting their presence on the surface. However, slip agents are, in general, not very soluble in water.
Other plasticizers, blooming agents, and processing additives in the polymer formulations can cause similar effects. Read more about the effects of slip agents and dyne pens here.
Watch the Video: Water Contact Angle vs. Dyne Inks
Best Alternatives to Dyne Testing
Our experience with thousands of bonding failures across hundreds of leading manufacturers reveals a surprising truth: the material or process is rarely to blame. Instead, these issues often stem from human decisions and complex environmental factors that traditional methods like dyne testing miss due to their limitations.
The industry needs a surface energy measurement that’s both sensitive and quick, taking less than two seconds and requiring minimal technical expertise.
Beyond Dyne Testing: A New Era in Surface Quality Control
For over a century, scientists have used water contact angle as a way to estimate surface energy because it offers significant advantages over traditional dyne testing:
- Precise and Objective Data: Water contact angle measurements provide quantitative, factual information about surface cleanliness and composition at the molecular level.
- Enhanced Quality Assessment: High sensitivity and accuracy allow for precise evaluation of surface
- Real-World Applicability: Unlike dyne testing, water contact angle is non-destructive and can be used directly on parts within manufacturing environments.
- Proactive Quality Control: Contact angle data serves as a measurable variable for Key Performance Indicators (KPIs) and Failure Mode and Effects Analysis (FMEA), enabling a more proactive approach to product development. This common measurement language improves communication and problem-solving, ultimately reducing costs.
- Centralized Insights and Collaboration: Water contact angle data integrates seamlessly with cloud-based surface intelligence networks like BConnect. This facilitates centralized analysis, enterprise-wide collaboration, and informed decision-making. BConnect offers real-time surface quality monitoring across production processes, functions, locations, and the entire supply chain. Stakeholders gain instant visibility into surface preparation and bonding, allowing them to maintain and demonstrate consistent quality standards at any location. This approach facilitates continuous process control, ensuring consistent cleanliness throughout production lines.
Download Your Personal Copy of This eBook
Fill out the form to receive your personal copy of the eBook, "What is Dyne Testing?"
Download the eBook Here
To take a deep dive into the best practices for improving surface quality & process control, read this eBook, "The Future of Manufacturing: A Guide to Intelligent Adhesive Bonding Technologies & Methodologies."