eBook
Metrics That Matter:
Quantifying Cleaning Efficacy for Manufacturing Performance
Contents
An Introduction to Mastering the Art of Industrial Cleaning
In today’s dynamic and regulated industrial cleaning landscape, ensuring consistent and verifiable cleanliness of products and components is not only a desirable ambition but a cornerstone of success. This imperative applies to all stakeholders within the industrial cleaning ecosystem--from manufacturers supplying parts to OEMs for assembly to producers of cleaning agents and cleaning equipment providers.
This comprehensive eBook delves into the intricacies of industrial cleaning and is intended to guide development teams, manufacturing engineers, and others tasked with developing or optimizing industrial cleaning processes and specifications. Whether your objective is defining precise cleanliness specifications or minimizing operating costs by reducing cleaning agent consumption and process complexity, adapting to evolving regulatory requirements, or creating precision-cleaned products for sensitive applications, this resource will empower you with the knowledge and tools to achieve these goals effectively.
By embracing these strategies, you can make informed decisions that pave the way for peak cleaning performance and ultimately, propel your business forward.
Download Your Personal Copy of This eBook
Fill out the form to receive your personal copy of the eBook.
Download the eBook Here
The Challenges of Controlling Industrial Cleaning
Within the industrial cleaning environment, numerous material surfaces and parts traverse intricate cleaning processes before undergoing subsequent downstream processes. These often involve customer assembly utilizing adhesive bonding techniques like sealing, painting, printing, or coating. Alternatively, your business may specialize in formulating and manufacturing cleaning agents for industrial cleaning applications. In both scenarios, achieving optimal cleaning performance hinges on establishing a meticulously calibrated balance between selecting the appropriate cleaning agents, understanding where non-obvious contamination may enter the process, and designing the correct cleaning process for optimal results.
Effectively navigating the challenges and solutions within industrial cleaning processes requires a holistic perspective. This necessitates understanding the critical role surfaces play throughout a product’s lifecycle, ensuring their cleanliness facilitates optimal performance and quality at each stage.
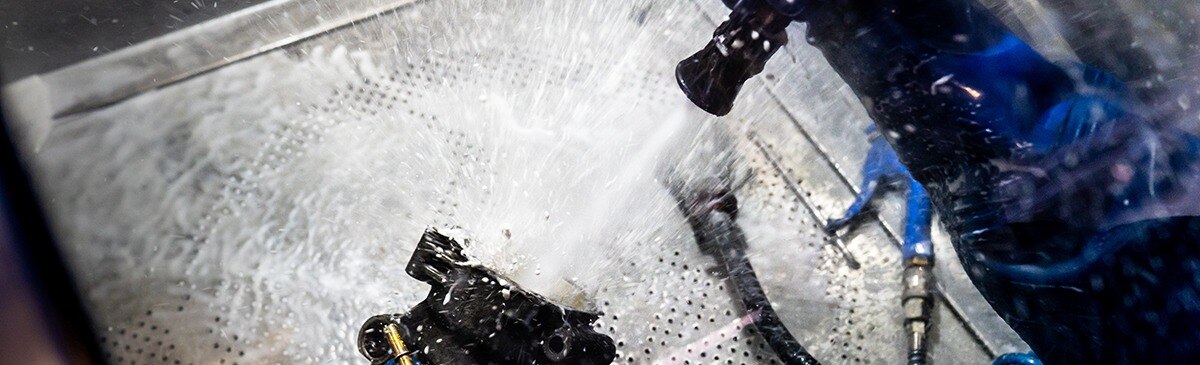
Ensuring Surface Cleanliness Optimizing Industrial Cleaning Operations with Surface Measurement
While the importance of surface cleanliness for a wide variety of processes is widely acknowledged, the specific requirements for achieving an appropriate level of ‘chemical cleanliness’ are often misunderstood.
Whether preparing surfaces for adhesion, plating, coating, brazing, welding, or even heat-treating - achieving optimal cleanliness extends beyond mere particulate removal, demanding meticulous attention to chemical contamination throughout the cleaning process is critical to success. These contaminants can originate from diverse and sometimes unexpected sources, posing significant challenges for professionals unfamiliar with the intricacies of surface science. Like those used in metal forming and shaping operations, cutting fluids and lubricants leave residues on the surface. However, did you know hand creams can also be a source of contamination that can become a barrier to optimal performance?
Determining whether a surface or part is clean means assessing surface quality including the component of chemical cleanliness.
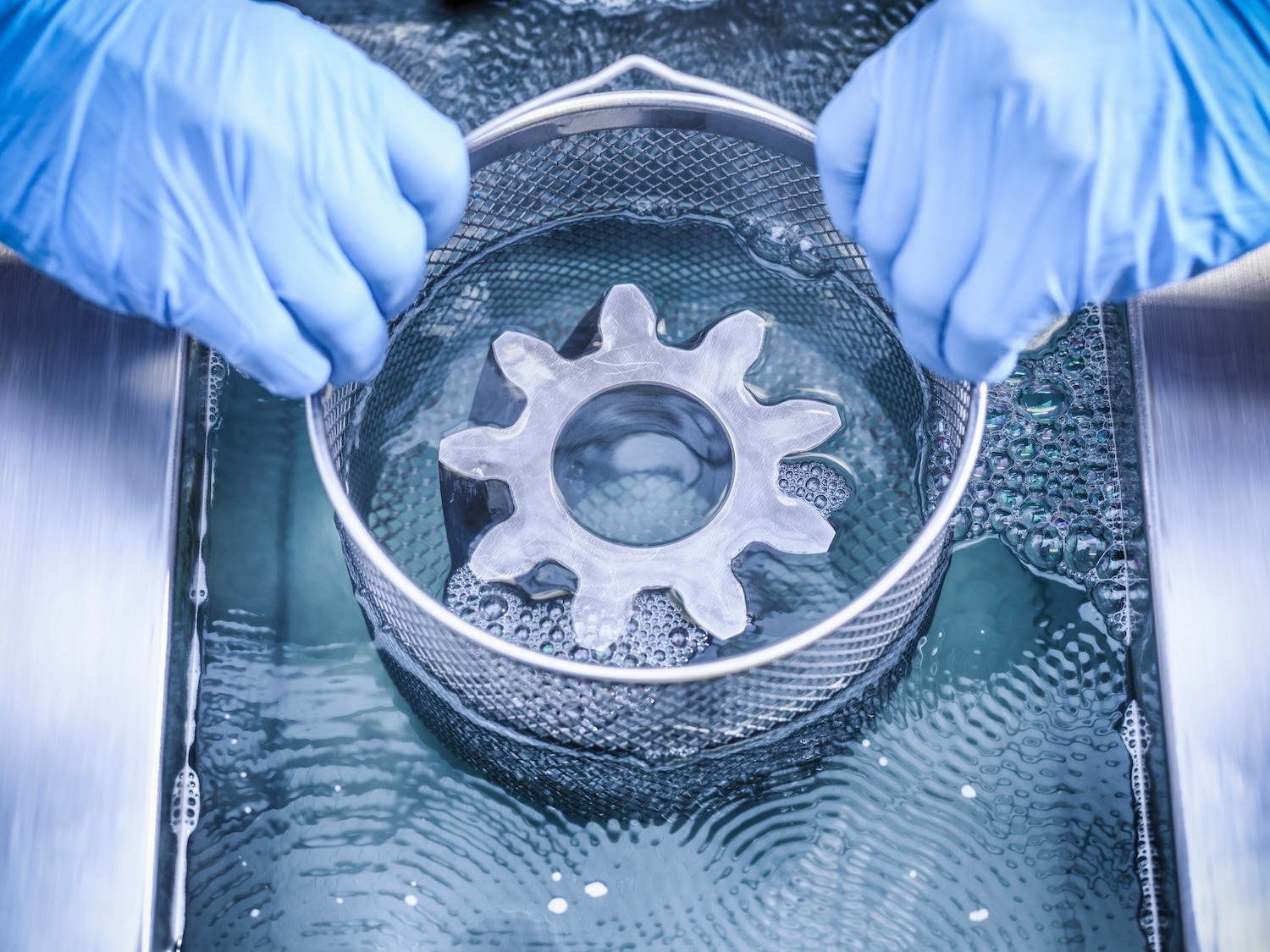
Common Industrial Cleaning Challenges
Cleaning Specifications Aren’t Comprehensive & Definitions of ‘Clean’ Vary
Historically, it has been very difficult to precisely measure chemical cleanliness, which has caused the industry to vary in their definitions of what clean means. In addition to not having the right technology readily available to directly measure surface cleanliness, manufacturers tend to lack Key Performance Indicators (KPIs) for their cleaning processes that are directly related to part cleanliness. Most KPIs monitor changes in cleaning solution (think PH or titration).
To try and manage these challenges, businesses will often under-clean, over-clean, or be in a state of process risk. If you over-clean a part ‘just to be sure’ that the part is thoroughly cleaned, this means costs are higher than needed. It also has implications for pricing because it’s hard to know what cleaning should cost.
However, did you know hand creams can also be a source of contamination that can become a barrier to optimal performance?
Ever-Changing Regulations
Cleaning processes bring a host of headaches, especially regarding workplace safety, disposing of wastewater, and forever cleaning chemicals. Complicating matters further, regulations change periodically, as recently with the EPA clamping down on PFAS “forever” chemicals. When cleaning is performed in-house, the business is responsible for meeting these challenges while achieving the surface cleanliness levels needed.
This article, "Navigating the Solvent Switch: A Sustainable Future for Parts Cleaning," explains how to make the switch from solvent cleaning to aqueous cleaning.
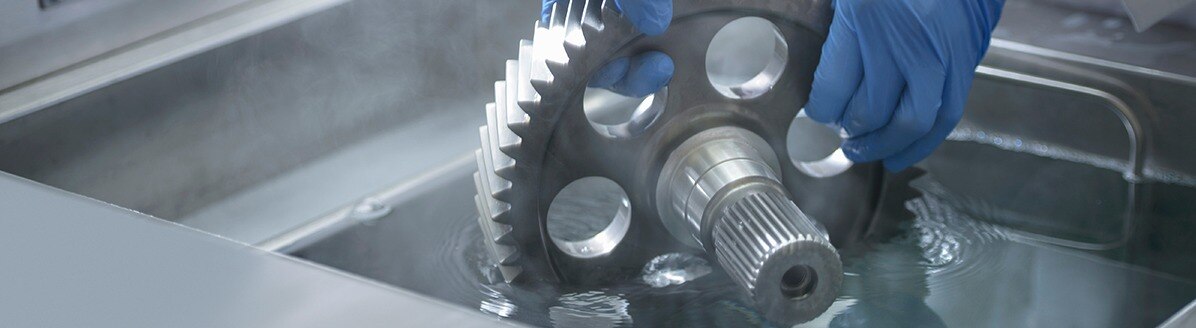
Not Knowing When to Change the Cleaning Chemistry & Filters
Because there hasn’t been an accurate way to measure cleanliness, knowing when to change the cleaning chemistry can be a significant challenge. Oftentimes, changes in cleaning chemistry are set by intervals, which are passed down through the organization by tribal knowledge.
Not Properly Managing Hidden Contamination
Many contaminants that can interfere with downstream processes are invisible to the eye, and even microscopic particles can cause problems down the line. Factors as mundane as human fingerprints and residues from upstream processes are common culprits.
Effective cleaning in industrial settings necessitates a multifaceted approach due to the diverse range of potential contaminants. Each contaminant, including oils, greases, lubricants, machining residues, and environmental particulates, possess unique properties requiring tailored cleaning strategies for optimal removal. The presence of contaminants, such as silicone, necessitates the implementation
of specialized cleaning techniques. This arises from their strong adhesion properties to surfaces, which significantly complicates their removal.
For companies that clean a wide variety of components from many different suppliers – there is added risk if customers change lubricants, packaging materials, or storage conditions. Being able to detect for these changes is important.
A lack of cleanliness measurement and definition can cause organizations to select the wrong type of cleaning method.
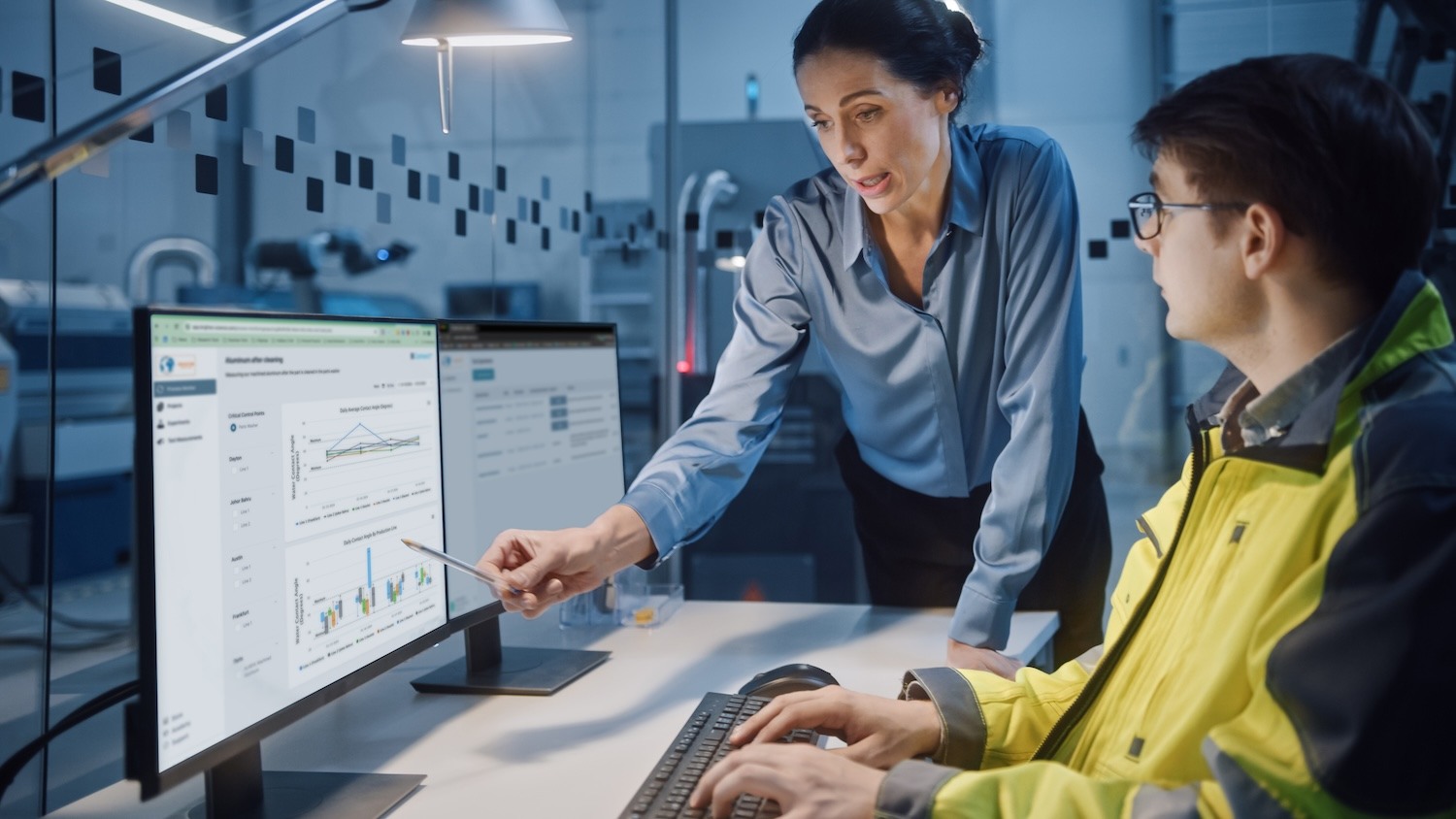
For example, a $400,000 piece of equipment may have been selected that only removes particulate contamination but doesn’t properly remove chemical contamination. Now, the company is stuck with an expensive piece of equipment that doesn’t actually work as intended.
Not Properly Managing Contamination on Incoming Parts
Robust quality assurance (QA) systems and standardized process approvals, such as the Production Part Approval Process (PPAP) or similar tools, which are essential for minimizing variability in incoming materials and ensuring surface cleanliness. While relying solely on supplier documentation offers a degree of convenience, it necessitates trust in their established procedures and carries the inherent risk of potential quality issues down the line.
A more significant concern is when identical parts are sourced from multiple suppliers or delivered from multiple plants owned by one supplier. In this situation, there’s an increased risk of variation in surface cleanliness. When dirty parts come in from a supplier, it may impact your already-defined cleaning process and may require significant adjustment to handle the variation effectively.
Implementing a risk-based approach that includes targeted inspections of incoming parts for cleanliness, even on a sampling basis, can significantly mitigate the negative impact of an uncleaned part.
Evaluating a New Cleaning Method
Effective cleaning needs to be fast and cost-effective while achieving the desired level of cleanliness. Different cleaning methods (solvents, aqueous solutions, mechanical) have varying levels of effectiveness against different contaminants and materials.
Choosing the wrong one can damage the surface or leave residues behind, which are later viewed as contamination and hinder adhesion performance.
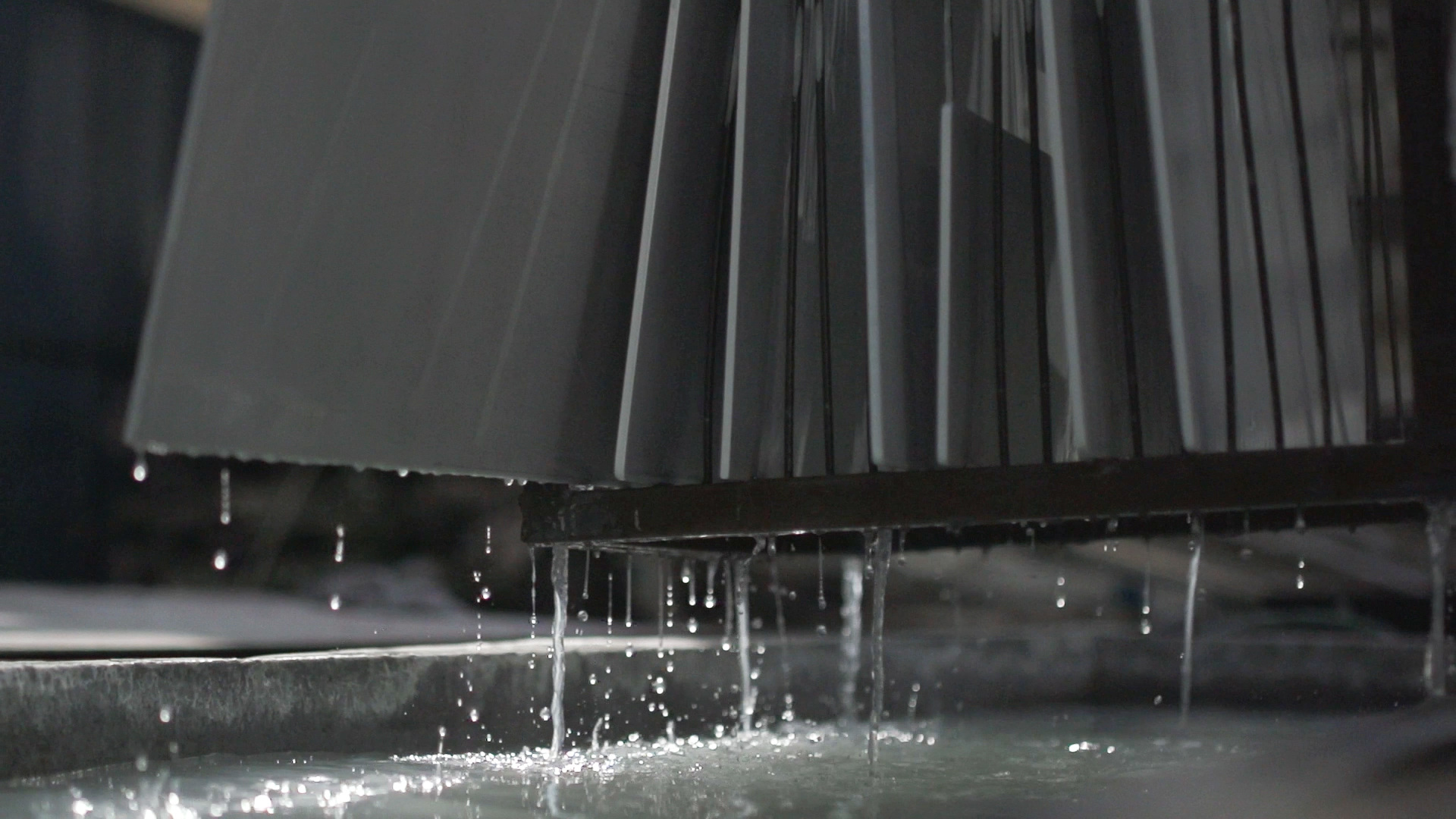
Effectively Cleaning Parts with Complex Geometry
Components that are complex in geometry and shape can be difficult to clean uniformly. The right testing method can validate whether these parts meet the
customer’s cleanliness specification or for a later bonding step.
Material Compatibility
Cleaning methods must be chosen carefully, as some solutions and processes can damage the materials being cleaned. For example, abrasives can mark softer materials like plastics, and acids damage aluminum and marble. Exposure to moisture harms wood surfaces.
When evaluating cleaning technologies, visual evaluation of cleanliness and even particulate counting is insufficient. Quantitative testing is needed to check for unwanted chemicals on the surface.
Production Line Integration
Manufacturers sometimes outsource component cleaning to avoid keeping up with regulatory challenges. However, this method requires verifying the cleanliness of incoming materials. The alternative is to clean in-house, and ideally, the process should be integrated into production without causing bottlenecks. This requires an in-line method of measuring cleanliness to avoid WIP inventory and the need for storage space.
Industrial Cleaning Optimization: Beyond Scheduled Maintenance
While industrial equipment requires regular maintenance, blindly following set schedules for filter, water, and chemistry replacements can be inefficient. While crucial for clean parts, this approach risks insufficient cleaning if replacements come too late. It also potentially wastes resources and incurs unnecessary costs by performing them too often.
Download Your Personal Copy of This eBook
Fill out the form to receive your personal copy of the eBook.
Download the eBook Here
The Risk of Getting it Wrong
When a cleaning process isn’t well controlled and measured, the consequences can be severe, affecting customers, the business, and the engineers responsible for the processes and equipment.
At the customer relationship level, the risk is that poor bonding or adhesion will result in complaints, warranty claims, and a damaged reputation. These consequences will almost certainly be deflected back to the manufacturer, and the loss of trust could affect the chances of winning future business.
Within the manufacturing organization, an inability to talk about cleanliness using a common language will result in disputes, disagreements, and even internal mistrust. These, in turn, will mean delays in the development and launching of new products, increased costs, and, as previously mentioned, customer blowback.
While everyone understands that mistakes happen, an individual's inadvertent wrong decision regarding part cleaning will have repercussions. Implementing proposals will take more time as management asks for more analysis, testing, and data, and individuals will have to endure association with a failed project or process implementation.
Common Measurement Solutions: Capabilities and Limitations
Achieving consistent surface cleanliness is a critical yet complex challenge that impacts product quality, customer satisfaction, and cost control. Engineers across diverse industries actively seeking solutions to gain control over this crucial factor. Here’s an overview of their key approaches today:
Iterative Process Development
This is where the team cleans a surface, following a defined process, and sees how well it performs. Examples of common testing include paint-wetting and tape pull-off tests to test adhesion.
If the tests are unsatisfactory (or there are field failures), that’s an indication that adjustments are needed. This might best be described as a “trial and error” approach. It’s slow and lacks quantification, objectivity, and sensitivity.
Common Measurement Methods
- Water break tests and dyne pens offer simple, low-tech However, their low sensitivity makes them easily swayed by even minor chemical contamination, limiting the reliability of high-precision bonding requirements. In addition to poor reliability, they are subjective and prone to false positives because they only provide a go/no-go result. Dyne solutions, in particular, can harm the environment and the users performing the test.
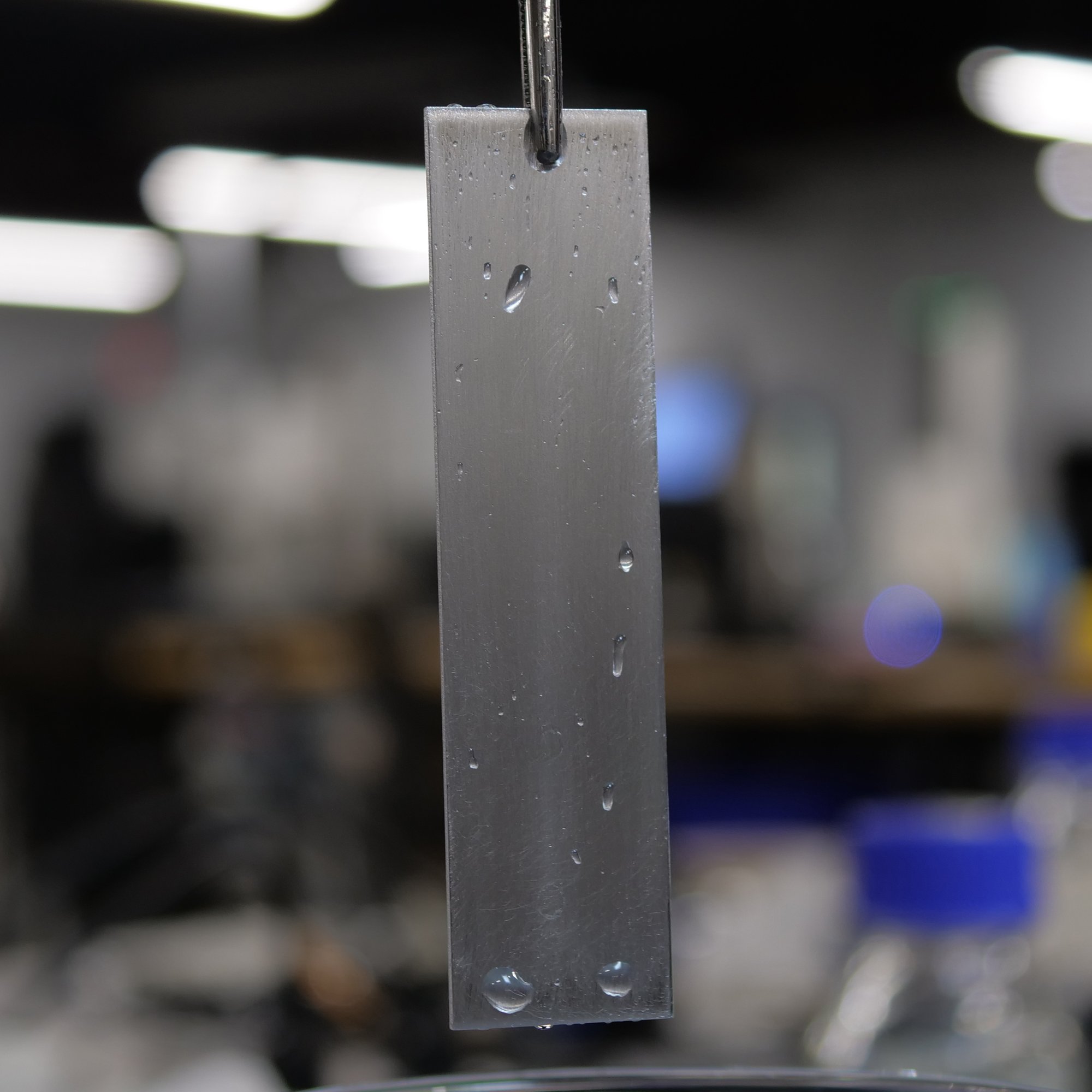
- Fluorescence, spectroscopy, and scanning electron microscopy (SEM) techniques delve deeper, requiring advanced equipment and expert operators.
Unfortunately, their complex nature restricts them to lab settings, hindering direct integration into production lines for continuous monitoring.
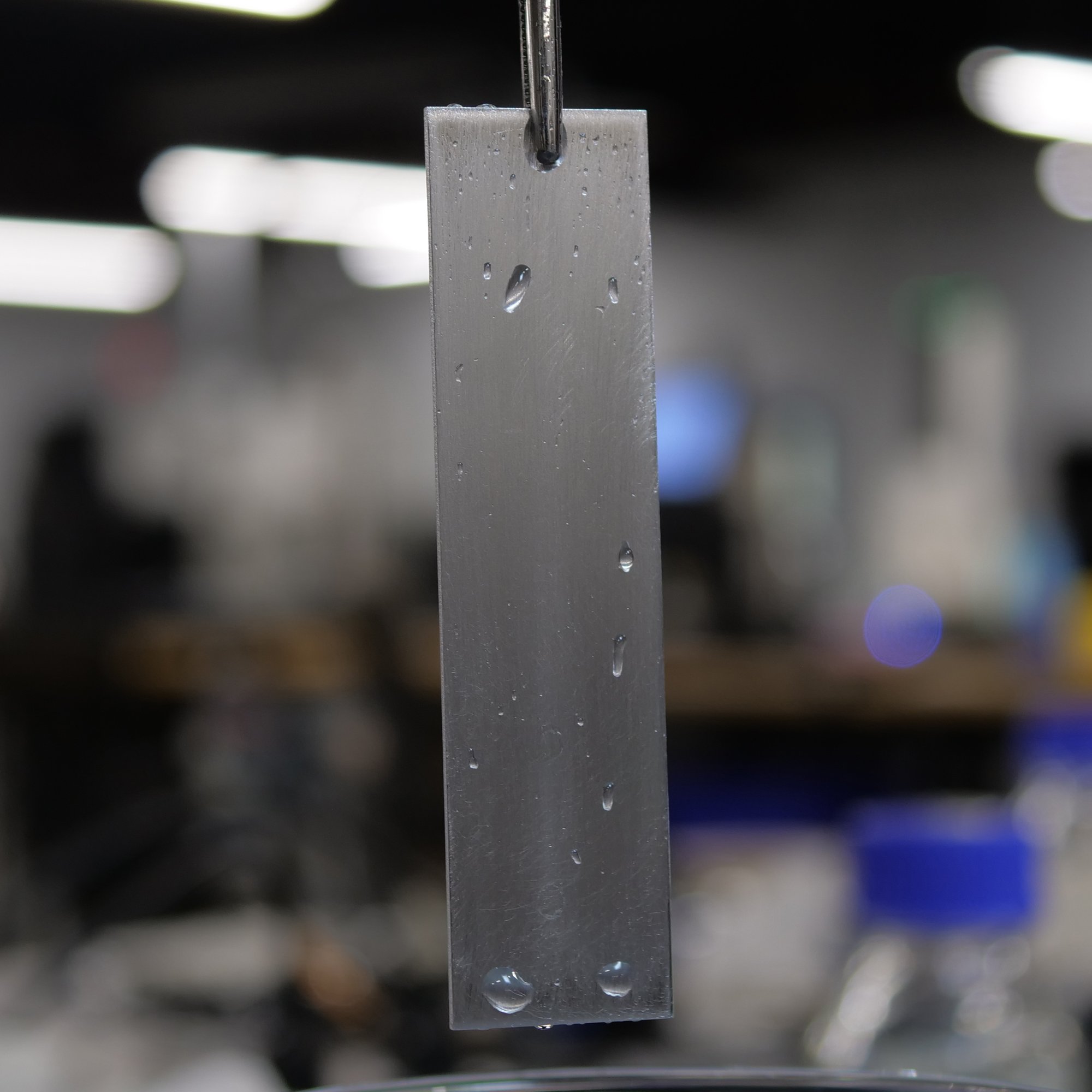
- Water Contact Angle stands out for its in-line, real-time measurement potential. Analyzing water droplet behavior on the surface translates contact angle into a numerical value reflecting surface energy. This method guarantees continuous process control, maintaining uniform cleanliness throughout production.
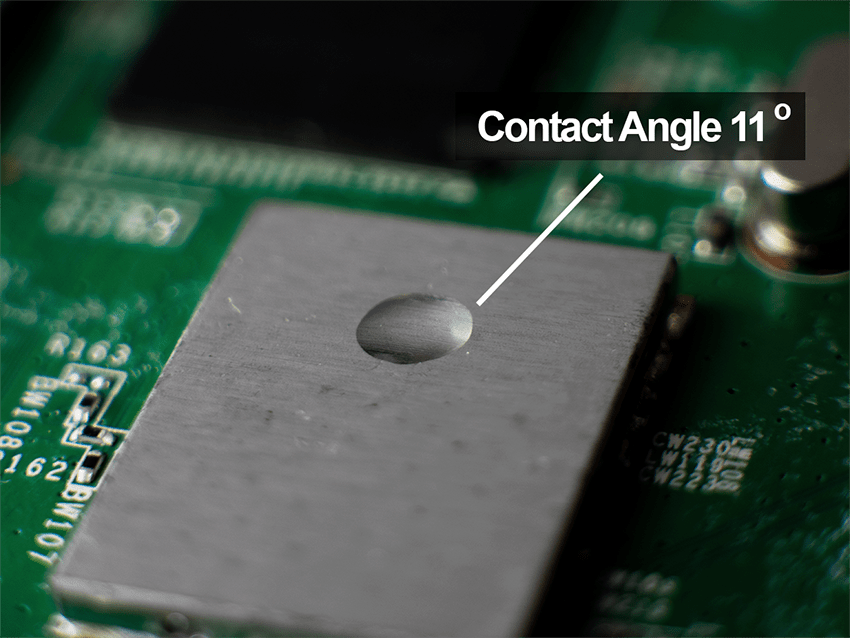
Indirect Measurements
Given the limitations of direct measurement, some manufacturers focus on implementing tight control over their cleaning processes by measuring process variables. Common methods used are testing PH levels of cleaning solutions, titration, and electrical resistance. The primary limitation of these methods is that they are all indirect measurements.
Given the complexity of chemistry involved in surface preparation and cleaning, there is a lag between when a problem occurs and when it’s identified, and it can give false positives that disrupt production.
Exploratory/R&D Efforts
Work is underway on using advanced software to develop methods of predicting surface cleanliness conditions. If successful, this could yield helpful tools and provide valuable process insights. However, as previously discussed, it requires data that can only be obtained from objective surface cleanliness measurements.
A Recommended Measurement Approach
To recap, chemical contamination on a surface will reduce the strength of bonds formed with coatings and adhesives. Therefore, it is essential to measure surface cleanliness and control the cleaning processes used. However, measuring cleanliness to the degree needed to detect contamination can be extremely complex. Fortunately, it’s not impossible. Water contact angle is a proven method of measuring surface cleanliness, but it must be used appropriately.
Here’s the recommended approach:
1. Identifying Contaminants for Effective Cleaning
An essential first step in selecting the appropriate cleaning method is determining what contaminants must be removed. By taking the time to identify and understand where contaminants enter the manufacturing process (via Critical Control Points), you can choose the correct cleaning method for the job, ensuring optimal results and efficient production.
2. Select a Cleaning Method
Cleaning methods are divided into solvents, aqueous solutions, and mechanical (plus a few others that don’t fit easily into these groups).
The efficacy of a cleaning process hinges on the judicious selection of a method aligned with the specific contaminants and desired level of cleanliness. With knowledge of the contaminants and their properties, surface scientists can recommend which method or methods will be most effective in achieving the required level of cleanliness.
Aligning the cleaning approach with the application’s specific needs can help organizations achieve optimal results and efficient production processes.
3. Optimize Process Parameters
This meticulous blueprint dictates critical parameters like temperature, pressure, flow rate, and chemical concentration. By precisely measuring and controlling these variables, consistency, and repeatability in achieving the desired level of cleanliness are ensured. In essence, it’s about doing it right every single time.
The second avenue, contamination prevention, tackles the challenge head-on by preventing contaminants from reaching surfaces in the first place. This proactive approach leverages a three-pronged strategy: education, training, and policies on acceptable and unacceptable materials.
Establishing and enforcing clear policies regarding acceptable and unacceptable materials and chemicals, such as prohibiting the use of hand cream by employees in sensitive areas of the production environment, serves as an additional layer of defense.
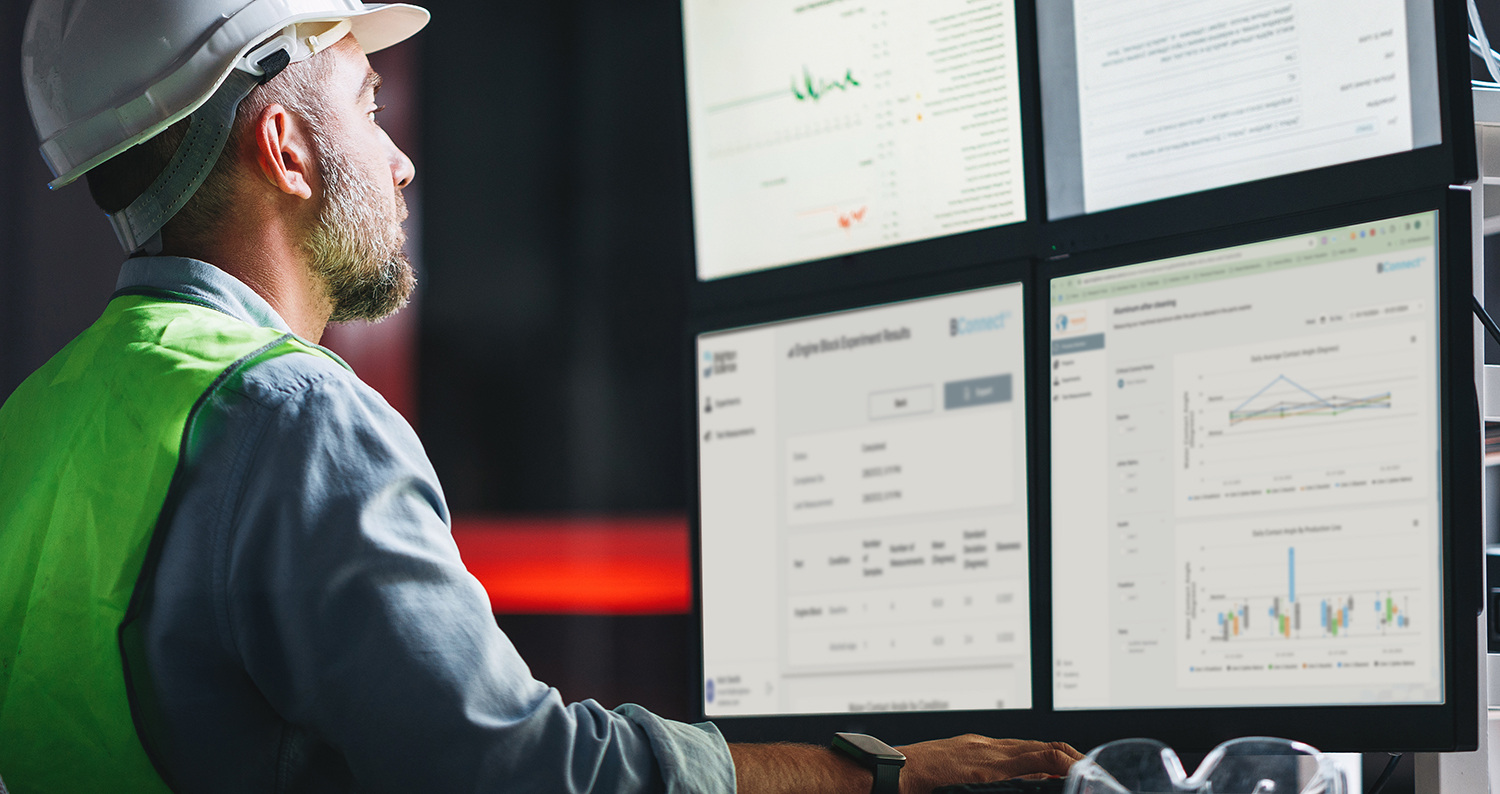
4. Quantifying Cleanliness
Achieving consistent surface cleanliness necessitates objective, data-driven assessment. Surface energy emerges as a powerful tool in this endeavor, a powerful method that delivers a quantifiable metric for direct evaluation. By leveraging intelligent technology, businesses can now approach surface cleanliness for critical processes like bonding, coating, and sealing with unwavering confidence at the very point of preparation.
This innovative approach translates into precise, numerical values that empower meaningful comparisons and meticulous control, particularly at Critical Control Points (CCPs) within the manufacturing process. No longer reliant on subjective observations, manufacturers gain access to invaluable data that unveils:
- Presence and location of potential contamination
- Trends and inconsistencies in cleaning performance
- Targeted opportunities for process
This transition to data-driven assessment paves the way for proactive contamination mitigation, consistent surface cleanliness, and, ultimately, elevated product quality.
5. Implement Statistical Process Control (SPC)
Achieving and maintaining consistent surface cleanliness transcends individual measurements. Statistical Process Control (SPC) is a critical tool in this pursuit, enabling engineers to monitor cleaning consistency and identify potential variations continuously. With intelligent solutions like BConnect, a networked Surface Intelligence platform, real-time surface quality data collection over defined maintenance intervals becomes a reality.
Through SPC analysis, trends and patterns in surface cleanliness readings are unveiled. This data-driven approach empowers engineers to:
- Proactively identify deviations from the established cleaning standard, indicating potential issues with the cleaning process or equipment performance.
- Optimize cleaning equipment maintenance schedules based on actual performance data rather than relying on fixed This can translate to cost savings and reduced downtime from unnecessary maintenance interventions.
- Implement preventative measures based on identified trends, addressing potential issues before they impact product quality or production efficiency.
6. Seamless Integration: Embedding Cleanliness Metrics in Production
Implementing a surface cleanliness measurement solution unlocks the potential for its seamless integration within the manufacturing process. This strategic integration:
- Reduces the risk of bottlenecks due to manual inspections or rework triggered by late-stage contamination
- Provides continuous feedback from automated measurements and optimizes the cleaning process in real-time, ensuring consistently clean surfaces without unnecessary over-cleaning, thereby enhancing overall production
- Facilitates easy data aggregation and analysis, empowering informed decision-making regarding process optimization, preventive maintenance, and resource allocation. This data-driven approach fosters continuous improvement and ensures peak cleaning process performance.
7. Embracing Sustainability
Industrial cleaning processes have a long history of generating unpleasant working conditions and hazardous wastes. Fortunately, the landscape is evolving, and cleaner, greener solutions are readily available.
But the question remains: how can we ensure these eco-friendly alternatives are as effective as their harsher, less sustainable counterparts?
This is where surface cleanliness metrics become crucial. By implementing quantifiable measurements, manufacturers can confidently navigate the sustainable cleaning landscape, achieving their environmental goals without compromising cleaning efficacy.
8. Continuous Improvement
The pursuit of unwavering cleanliness and cost efficiency requires a commitment to continuous improvement. Integrating a surface cleanliness measurement solution like BConnect gives manufacturers the crucial data needed to drive this pursuit. With BConnect in place, manufacturing facilities have the numbers needed to optimize cleaning costs and performance. Sharing the data internally or with external process experts will set an improvement effort in motion.
Benefits of the Surface Energy Measurement Approach
Surface energy measurement yields precise and repeatable numbers that reveal the cleanliness of surface molecules to form bonds with adhesives, sealants, and other coatings. It is the only technology to allow trend monitoring and provide actionable warnings when problems are developing.
The solution offered by Brighton Science is:
- Suitable for industrial use – it does not involve sending samples to a lab
- Fast – for the reason given above
- Adaptable for differing product and material geometries
- Non-destructive
- Non-hazardous to humans
- The basis of a common language between teams, departments, customers and suppliers
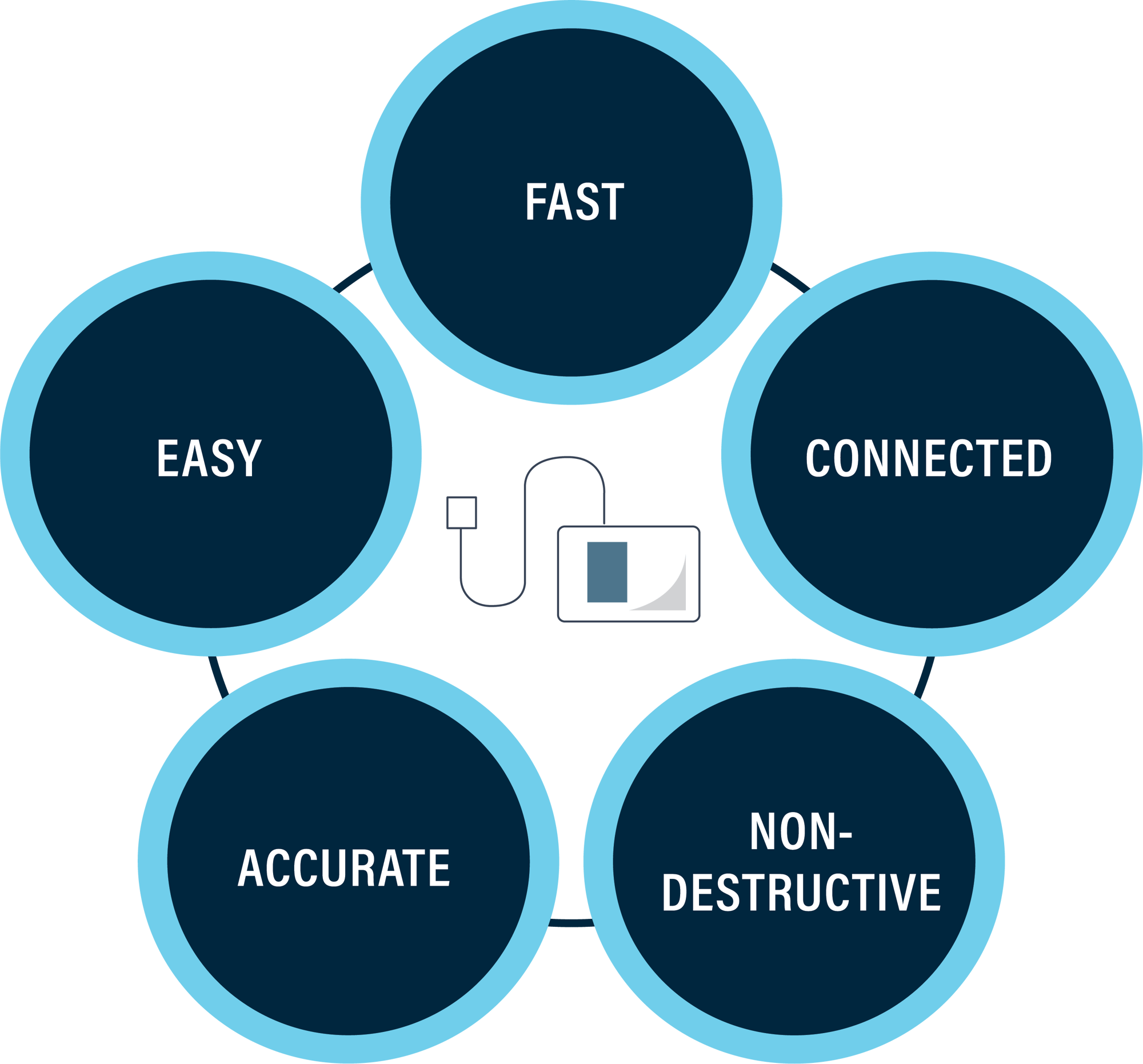
For any manufacturer seeking to improve control over coating and bonding processes, the best solution, for the reasons discussed previously, is to measure surface energy. This can be done continuously with in-line automation, enabling real-time data to be shared immediately.
Water contact angle measurement technologies are not all the same, nor are their capabilities. BConnect’s data and analysis are unique and provide users with the intelligence needed to move ahead of competitors.
Next Steps
At this point, a degree of skepticism is to be expected. Many companies have proposed ways of assessing the cleanliness of surfaces for chemical bonding. While some offer real benefits, all have limitations. The only solution proven to yield actionable data is BConnect.
If a demonstration would be more convincing, request a demonstration of BConnect. Alternatively, request a quotation or speak to an expert.