eBook
Beyond Cleaning Chemistry:
Improving Bath Management with Analytics-Driven Surface Quality Control
Contents
Cleaning agents can be cheap, but poor cleaning performance is expensive!
It's a common misconception that cleaning agents are a major expense in metal finishing operations. While the chemistry cost for a typical operation may be around 7-10%, cleaning chemistries actually make up a relatively small percentage of the total cost. However, the real impact on your bottom line lies in the consequences of poor cleaning.
When cleaning processes fail, it leads to a cascade of problems that can significantly increase costs and disrupt operations. Rework, scrap, defects, downstream contamination, downtime, and waste removal are just a few of the potential pain points. These issues' exact nature and severity will vary depending on the specific process, but in most cases, the most significant pain is the loss of productivity caused by having to "get things right" again.
During a recent webinar titled The Surface Tells All, industry experts Lucas Dillingham from Brighton Science and Mike Valenti from Hubbard Hall discussed innovative measurement methods and analytics designed to improve bath life, control cleaning chemistry, and validate surface cleanliness.
Discover how these insights are opening new dimensions in process control, offering manufacturers precise solutions for spec development and problem-solving.
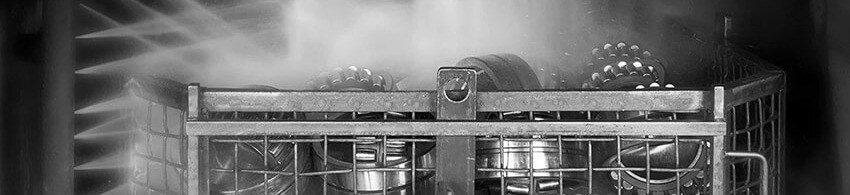
Why Surface Cleanliness Matters
When it comes to metal finishing, adhesion processes like electroplating, anodizing, or powder coating are often viewed as the core of value creation. However, surface preparation before these processes is equally crucial. Without proper cleaning, the quality and performance of these finishing processes are at risk.
Valenti noted, "If you don't get it right in those first process steps, you're not going to get good results in all the tanks where you actually make money."
Whether it's ensuring corrosion resistance or achieving a decorative finish, cleaning is the 'tip of the spear' that initiates the chain of production value.
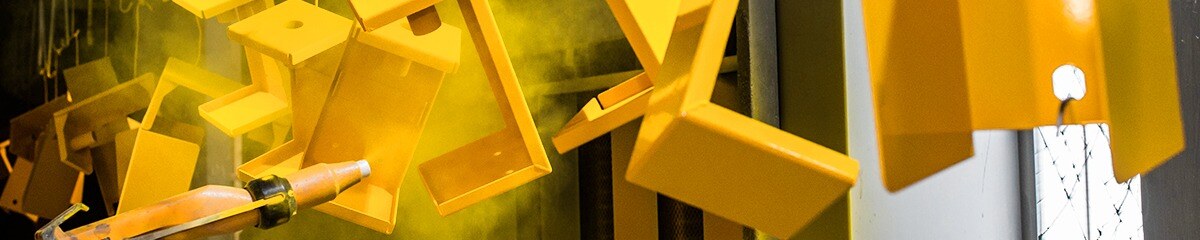
Traditional Control Methods Offer A Limited View
Historically, the assessment of quality control in metal finishing has primarily relied on chemical titration and conductivity methods. These techniques focus on the quality of the bath's chemistry by measuring the concentration of specific chemicals within the cleaning bath, providing only a snapshot of the whole picture. This approach offers a limited view of the overall bath's performance because it doesn’t account for what’s present on the surfaces of the parts being cleaned. This can lead to situations where the chemistry is ‘in spec’ on paper, but the parts themselves aren't meeting cleanliness standards.
While these methods can be useful for monitoring certain aspects of bath chemistry, they have several significant drawbacks including:
Limited Chemical Analysis
By focusing solely on a few chemical components, these methods overlook other additives, such as surfactants and detergents, that play a crucial role in cleaning effectiveness.
No Soil Removal Information
Traditional control processes fail to provide insights into the amount of contamination removed from the parts. This is a critical factor, as the removed soil must go somewhere, often entering the cleaning bath itself.
Measurement Variation
These methods can be subject to significant measurement variation, making it difficult to accurately assess bath performance. Factors such as operator error, probe contamination, and subjective interpretation can hinder the reliability of results.
Lack of Correlation with Part Quality
Measurements of chemistry are not always predictive of part quality. Even a bath with all measurements within statistical limits can still produce defective parts. This highlights the limitations of relying solely on chemical analysis for surface quality control.
Additionally, oil load tests, another traditional method, also have their shortcomings. Aqueous oil load tests often require subjective interpretation, while solvent-based tests can be complex and difficult to monitor. Moreover, many operations do not observe a significant rise in boiling point, indicating that oil load may not be a major issue. These tests are often run infrequently and are not suitable for real-time bath maintenance.
These methods are often reactive rather than proactive, subjective, and fail to account for the critical role of rinsing in preventing contamination. Relying solely on these methods can lead to suboptimal surface quality control, increased costs, and rework.
To achieve optimal results, exploring more advanced and comprehensive approaches is essential.
While traditional methods should not be abandoned entirely, they should be complemented with direct part measurement to gain a more holistic and complete picture of bath performance. By adopting a more modern and data-driven approach, businesses can improve their surface quality control efforts and achieve significant benefits.
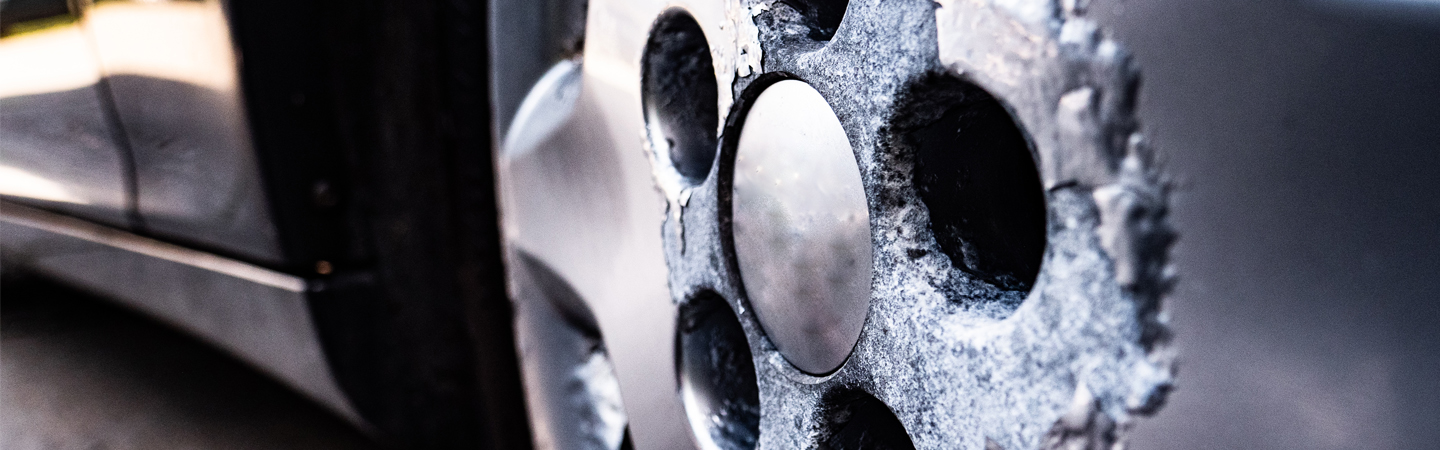
Measuring Surface Cleanliness
Historically, organizations have assessed surface cleanliness using subjective and destructive methods such as dyne test fluids and water break tests. These methods rely on visual observations of how liquids interact with the solid surface. However, these approaches are often inaccurate and fail to provide a quantitative assessment of surface conditions.
Water break tests are often used to assess surface cleanliness. However, these tests can be misleading. For example, a passing water break test may not indicate a truly clean surface if hydrophilic contaminants are present. These contaminants can be difficult to detect using traditional methods but can still cause problems downstream.
A more effective and modern approach is to measure water contact angle (WCA) in production. WCA provides a quantitative and objective assessment of surface cleanliness. Unlike traditional methods, WCA can detect both hydrophobic and hydrophilic contaminants, giving a more complete picture of surface conditions. WCA offers several advantages over traditional methods including:
- Quantitative Measurement: WCA provides a numerical value that can be used to objectively assess surface cleanliness.
- Detection of Both Hydrophobic and Hydrophilic Contaminants: WCA can detect a wider range of contaminants, including both hydrophobic and hydrophilic substances.
- Dynamic Wetting Properties: WCA can measure the dynamic wetting properties of the surface, providing insights into the interaction between the surface and the liquid.
- Automation: WCA measurements can be automated, making them more efficient and reliable.
Read more about the limitations of water break tests, "The Water Break Test as a Surface Measurement Gauge."
Case Study: Rapid Cleaning Solution Selection for Nickel Alloy Substrates
Due to impending environmental regulations, a manufacturing company faced the challenge of replacing its existing cleaning solution for nickel alloy substrates.
The company required a new solution that could effectively remove contaminants while maintaining the desired level of cleanliness and meeting regulations. The traditional method of assessing new chemistries often involved lengthy trial-and-error processes, leading to significant time and resource expenditures.
-1.png?width=1000&name=chart-and-title%20(1)-1.png)
The chart above illustrates the effectiveness of a new cleaning solution for a nickel alloy substrate. The x-axis represents the water contact angle (WCA), a measure of surface hydrophobicity, while the y-axis represents the carbon-to-nickel ratio, indicating the relative amounts of these elements on the surface
Initial Surface Condition
Prior to cleaning, the nickel alloy parts exhibited a high water contact angle (around 80 degrees) and a high carbon-to-nickel ratio. This indicates a hydrophobic surface with significant contamination.
Impact of Cleaning
By implementing various cleaning chemistries, temperatures, and times, they were able to significantly reduce the water contact angle and decrease the carbon-to-nickel ratio. When the WCA reached 15-18 degrees, the carbon-to-nickel ratio was approximately 1:1, suggesting a cleaner surface.
Time and Cost Savings
This data-driven approach allowed them to optimize the cleaning process within a short timeframe. In this case, a process that would have normally taken six months was completed in just six weeks, demonstrating the efficiency and effectiveness of using WCA measurements to guide cleaning operations.
Conclusion
This chart highlights the sensitivity and accuracy of WCA measurements in assessing surface cleanliness. By using WCA data, organizations can optimize their cleaning processes, reduce costs, and improve overall product quality.
Process Health Monitoring: Optimizing Finishing Processes Through Real-Time Monitoring
High-volume finishing lines often involve a series of pre-treatment steps, culminating in the final finishing process, also known as the "money tank," where value is added to the part and a substantial increase in its overall cost.
By implementing a robust monitoring system that tracks key parameters throughout the finishing process, businesses can significantly reduce costs, save time, and minimize waste by identifying potential issues early on.
A multi-step process health monitoring approach might include:
- Incoming Material Inspection: Regular testing of incoming materials to detect any changes in composition or surface properties that could impact the finishing process.
- Process Monitoring: Continuous tracking of critical process variables, such as chemical concentrations, temperature, and cleaning times, to ensure consistent performance.
- Surface Analysis: Regular evaluation of the part surface before and after each processing step to assess the effectiveness of cleaning and pretreatment operations.
Relying solely on titrations for tank monitoring can lead to significant problems. Titrations provide a limited view of the bath's performance and may not detect issues until it's too late, resulting in the production of large quantities of defective parts.
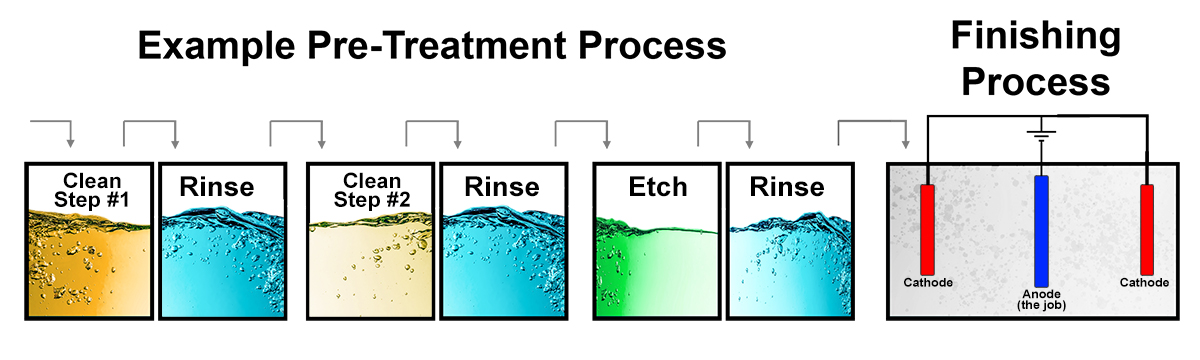
The image above depicts an example of a typical high-volume finishing operation with the final tank, often referred to as a 'money tank.' Examples of common finishing processes or 'money tanks' include plating, anodizing, fast-fading, or powder coating processes.
The Importance of Incoming Inspection
Many operations clean their tanks on a regular schedule. However, this approach can be ineffective if the cleanliness of the incoming parts is not monitored. The volume of parts processed each week can vary, impacting the effectiveness of the cleaning chemistry. Implementing an incoming inspection can help:
- Maintain Consistent Cleaning: By assessing the cleanliness of incoming parts, you can adjust the cleaning process accordingly, ensuring optimal performance.
- Proactive Control: Incoming inspection allows you to identify potential issues early on, preventing problems from escalating and affecting the final product.
- Schedule Optimization: By understanding the cleanliness of incoming parts, you can optimize the cleaning schedule to ensure efficient and effective tank maintenance.
Case Study: The Impact of Unknown Supplier Changes on Cleaning Operations
A stamped steel powder coating line experienced issues with iron phosphate not forming correctly on the surface. Despite the client's belief that its process had not changed, it was discovered that its raw material steel supplier had switched lubricant suppliers. The new lubricant left a more tenacious residue on the steel, hindering the iron phosphate coating and causing the final powder coating to fail.
To overcome this issue, a new cleaning solution was required. By analyzing water contact angle (WCA) data, the client was able to quickly choose a cleaning chemistry that could effectively dissolve the residual lubricant instead of simply displacing it.
By assessing the surface quality of incoming raw materials and making necessary process adjustments, operations can ensure consistent product quality and proactively manage their supply chains.
Measurement Methods and the Future of Surface Preparation
Surface preparation is a multifaceted process. It's not just about removing visible particles or dirt; it's about addressing contaminants on a molecular level. We see that 90% of failures are due to poor surface preparation. While physical debris is often easy to spot and remove, molecular-level contamination can go unnoticed for a long time and result in product failure if not adequately addressed.
This is where new measurement methods, such as water contact angle technology, come into play. Brighton Science developed the world's first fully handheld, portable system that objectively measures surface cleanliness by assessing water contact angles on parts during production. This innovation allows engineers to make informed decisions about when to change their cleaning chemistry or address potential issues before they affect the final product.
By measuring the wettability of a surface, this method provides a real-time, quantifiable assessment of surface cleanliness. The insights gained allow for better control over processes, minimizing waste, reducing rework, and ensuring that surfaces are properly prepared for subsequent steps in production.
Bridging the Knowledge Gap with Analytics
One of the critical gaps in surface preparation has been the lack of real-time data. Companies have been forced to rely on subjective tests like water break or dye penetrant tests, which don't provide precise, actionable data. With Brighton Science's water contact angle technology and their cloud-connected platform, BConnect, manufacturers now have access to digital, data-driven insights that allow for proactive decision-making.
This system provides instant feedback and documentation, offering manufacturers a "digital thread" that tracks every critical control point throughout the production process—from incoming material to the final finish. It's a step forward in bridging the surface quality knowledge gap that has plagued the industry for years.

Image Above: A depiction of a simple manufacturing process, demonstrating how operations can deploy sensors, testing procedures, and network monitoring to monitor critical control points throughout the production line and across multiple global plant locations, ultimately leveraging the power of surface quality control.
From Random Rework to Consistent Success: The Power of Surface Analysis
Surface cleanliness may seem like a small detail, but it's a foundational element that drives overall product quality and performance. Proper surface preparation is critical to achieving success, whether you're involved in metal finishing, bonding, or painting.
The future of manufacturing lies in embracing new analytics and measurement methods. By understanding and controlling surface cleanliness at a molecular level, companies can reduce costs, improve product quality, and unlock new levels of efficiency in their processes.
If you're ready to take control of your surface preparation and ensure better outcomes, technologies like Brighton Science's Surface Analyst and the BConnect platform are transforming the way we think about cleanliness. As Dillingham stated in the webinar, "If you've ever struggled with random rework or failure, it's probably due to poor surface preparation—so let's fix that."
Watch the full webinar "The Surface Tells All - An Analytics-Driven Approach to Better Bath Management."
To learn how your organization can leverage surface quality data to optimize cleaning and finishing processes, download the eBook "Metrics That Matter: Quantifying Cleaning Efficacy for Manufacturing Performance."